Share this
Lean Kanban A Complete Guide For Digital Leaders
by Luis Gonçalves on Jan 13, 2024 6:06:38 AM
Lean Kanban is a popular agile framework that originated from Toyota's manufacturing process in the 1940s. Combining the Lean methodology's focus on eliminating waste with the Kanban system's visual workflow management, Lean Kanban has evolved into a powerful tool for teams across various industries to optimize their work processes.
ADAPT Methodology® is a unique Digital Product Development framework to change traditional project-centric companies toward product-led companies!
Society changed and leaders need support in the way how they lead and design their digital product organizations, that is the reason why the ADAPT Methodology® was created, but now let’s get a deep dive into the “Lean Kanban” topic.
Benefits of Implementing Lean Kanban
Implementing Lean Kanban can offer several benefits, including improved efficiency, reduced lead times, increased visibility into work processes, and a stronger emphasis on collaboration and continuous improvement. It also helps teams better manage their workload by limiting work in progress (WIP) and prioritizing tasks based on their importance and urgency.
Understanding the Principles of Lean Kanban
Lean Kanban is built on six core principles that drive its effectiveness.
Visualizing Work
One of the key principles of Lean Kanban is to visualize work by representing tasks, workflows, and progress on a Kanban board. This visual representation helps teams gain a better understanding of their work process and identify bottlenecks and areas for improvement.
Limiting Work in Progress
Limiting WIP is essential to prevent multitasking, reduce stress, and increase focus. By limiting the number of tasks being worked on simultaneously, teams can concentrate on completing work items efficiently and effectively.
Managing Flow
Lean Kanban emphasizes the importance of managing the flow of work through the system. Teams should focus on reducing wait times, minimizing blockers, and ensuring a smooth flow of tasks from start to finish.
Making Process Policies Explicit
To ensure that everyone is on the same page, Lean Kanban encourages teams to make their process policies explicit. This includes defining the criteria for moving tasks from one stage to another and establishing rules for assigning work.
Implementing Feedback Loops
Feedback loops, such as daily stand-ups and retrospectives, are crucial for continuous improvement. They help teams identify issues, learn from their experiences, and adapt their processes accordingly.
Collaborative Improvement and Experimental Learning
Lean Kanban promotes a culture of collaboration and experimental learning. Teams should work together to identify and implement improvements, test new ideas, and learn from both successes and failures.
Lean Kanban in Practice
The Kanban Board
A Kanban board is the primary tool used to visualize and manage work in Lean Kanban. The board typically consists of the following components:
Columns and Swimlanes
The Kanban board is divided into columns that represent different stages of the work process (e.g., To Do, In Progress, and Done) and swimlanes that separate different types of work or priorities.
Work Item Cards
Tasks are represented as cards on the board, with each card containing important information such as the task's title, description, priority, and deadline. Team members can easily move cards across columns as they progress through the workflow.
Pulling Work Through the System
In Lean Kanban, team members "pull" tasks from one column to the next, rather than having tasks "pushed" onto them. This approach ensures that team members only work on tasks when they have the capacity to do so and helps maintain a smooth workflow.
The WIP Limit
The work in progress (WIP) limit is a key element of Lean Kanban. It restricts the number of tasks that can be in progress in each column or swimlane. By adhering to the WIP limit, teams can better manage their workload and focus on completing tasks efficiently.
Metrics and Reporting
Lean Kanban relies on various metrics to monitor and improve team performance. Common metrics include lead time (the time it takes for a task to move from start to finish), cycle time (the time it takes to complete a task once it's started), and throughput (the number of tasks completed in a given time period). Teams can use these metrics to identify areas for improvement and track progress over time.
Scaling Lean Kanban
Lean Kanban can be scaled to accommodate larger organizations or complex projects by adding additional layers of hierarchy, such as program or portfolio Kanban boards. These higher-level boards can help coordinate work across multiple teams and align strategic goals with day-to-day operations.
FAQs
- What is the difference between Lean Kanban and traditional Kanban?
While both Lean Kanban and traditional Kanban use visual boards to manage workflow, Lean Kanban incorporates additional principles from Lean methodology, such as eliminating waste, continuous improvement, and focusing on value delivery.
- Can Lean Kanban be applied to non-manufacturing industries?
Yes, Lean Kanban is highly versatile and can be applied to various industries, including software development, marketing, finance, and more.
- How does Lean Kanban help with prioritization?
Lean Kanban encourages teams to prioritize tasks based on their value and urgency. This can be done through the use of swimlanes, color-coding, or other visual cues on the Kanban board.
- What is the role of the WIP limit in Lean Kanban?
The WIP limit helps teams manage their workload by restricting the number of tasks that can be in progress at any given time. This prevents multitasking, reduces stress, and promotes a smoother workflow.
- How do feedback loops contribute to continuous improvement in Lean Kanban?
Feedback loops, such as daily stand-ups and retrospectives, provide teams with regular opportunities to identify issues, discuss possible improvements, and adapt their processes based on their experiences and learnings.
Conclusion
Lean Kanban is a powerful project management and productivity framework that combines the principles of Lean and Kanban to help teams visualize their work, limit WIP, and continuously improve their processes. By implementing Lean Kanban, teams can enjoy increased efficiency, reduced lead times, and a stronger focus on collaboration and learning.
FAQs
- What is the difference between Lean Kanban and traditional Kanban?
While both Lean Kanban and traditional Kanban use visual boards to manage workflow, Lean Kanban incorporates additional principles from Lean methodology, such as eliminating waste, continuous improvement, and focusing on value delivery.
- Can Lean Kanban be applied to non-manufacturing industries?
Yes, Lean Kanban is highly versatile and can be applied to various industries, including software development, marketing, finance, and more.
- How does Lean Kanban help with prioritization?
Lean Kanban encourages teams to prioritize tasks based on their value and urgency. This can be done through the use of swimlanes, color-coding, or other visual cues on the Kanban board.
- What is the role of the WIP limit in Lean Kanban?
The WIP limit helps teams manage their workload by restricting the number of tasks that can be in progress at any given time. This prevents multitasking, reduces stress, and promotes a smoother workflow.
- How do feedback loops contribute to continuous improvement in Lean Kanban?
Feedback loops, such as daily stand-ups and retrospectives, provide teams with regular opportunities to identify issues, discuss possible improvements, and adapt their processes based on their experiences and learnings.
Did you like this article?
We enable leaders to become highly valued and recognized by adapting their project-centric company into a product-led company, society changed and leaders need support to adapt their companies to the digital era, that is the reason why the ADAPT Methodology® was created!
If you are interested in knowing if your company is a project-centric or a product-led company simply take our Project To Product Scorecard.
If you want to know how we can help you to start your transformation please check out our: Project To Product Training.
If you are interested in doing a transformation in your company please check out our: Project To Product Consulting.
Share this
- Agile Methodologies (18)
- Product Strategy (18)
- OKRs (16)
- Scrum (16)
- Product Mindset (14)
- Project To Product (10)
- Agile Retrospectives (9)
- CoPs (9)
- Knowledge Sharing (9)
- Time To Market (8)
- Product Discovery (7)
- Continuous Improvement (5)
- Strategy (5)
- Scrum Master (4)
- Content Marketing Strategy (3)
- Product Owner (3)
- Technical Excellency (3)
- Digital Transformation (2)
- Innovation (2)
- Scaling (2)
- Team Building (2)
- Business Model (1)
- Cost Of Delay (1)
- Customer Feedback (1)
- Customer Journey (1)
- Customer Personas (1)
- Design Thinking (1)
- Digital Leadership (1)
- Digital Product Tools (1)
- Go To Market Strategy (1)
- Google Design Sprint (1)
- Lean Budgeting (1)
- Lean Change Management (1)
- Market Solution Fit (1)
- Organisational Impediments (1)
- Outsourcing (1)
- Product (1)
- Product Metrics (1)
- Product Roadmaps (1)
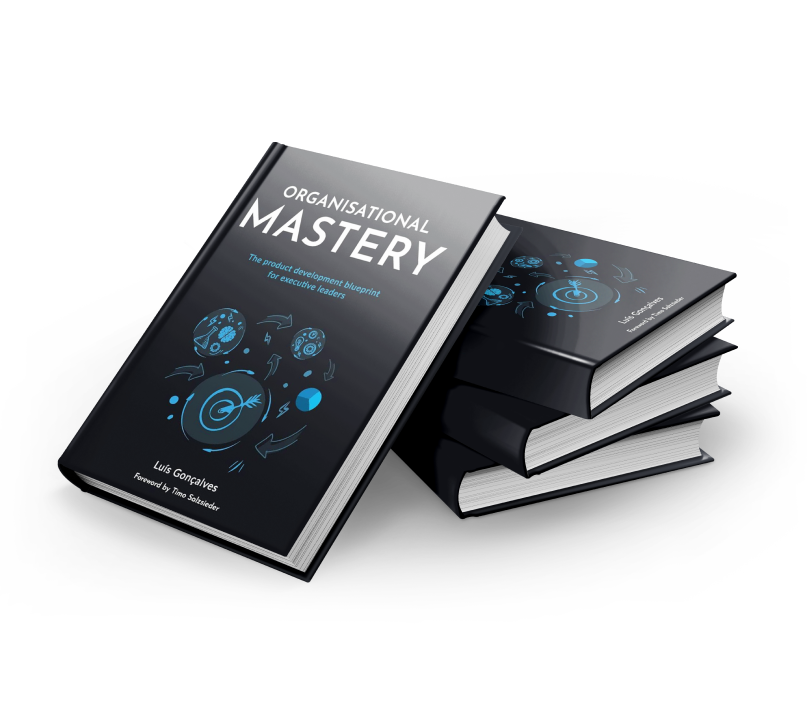
Organisational Mastery
Get your free copy
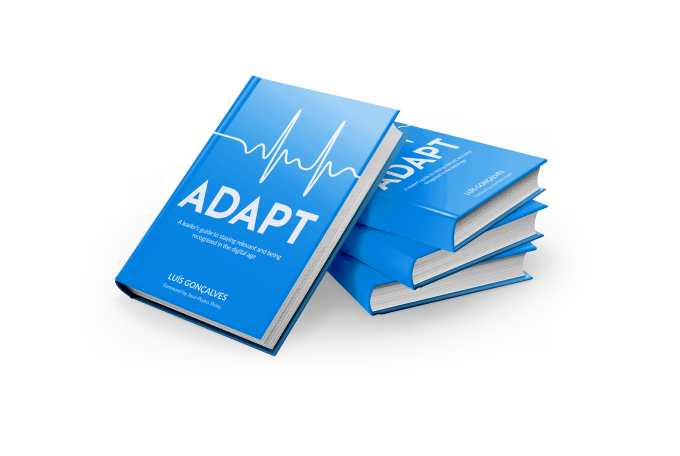
ADAPT
Get your free copy
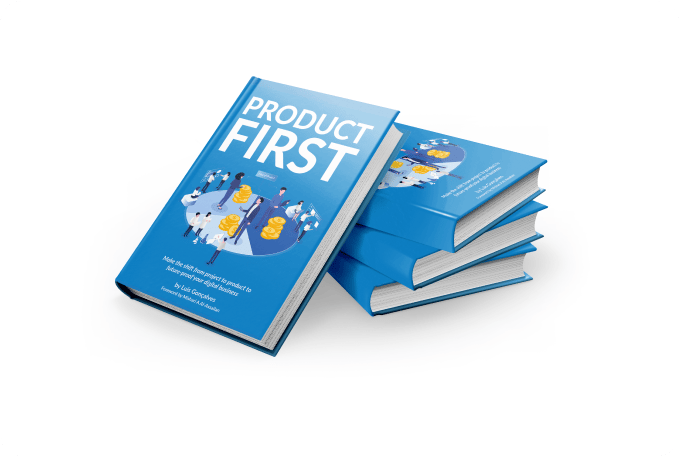
Product First
Get your free copy